Chains are Made with Various Processes
World quality chains are born from the high-level quality management system of Hamanaka Chain Mfg. Co., Ltd.
Below is the introduction of the manufacturing process.
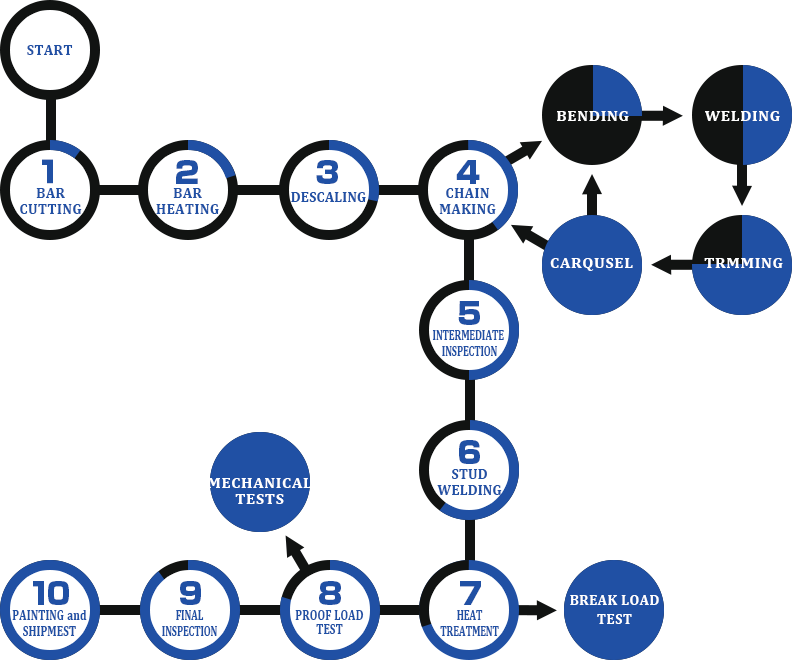
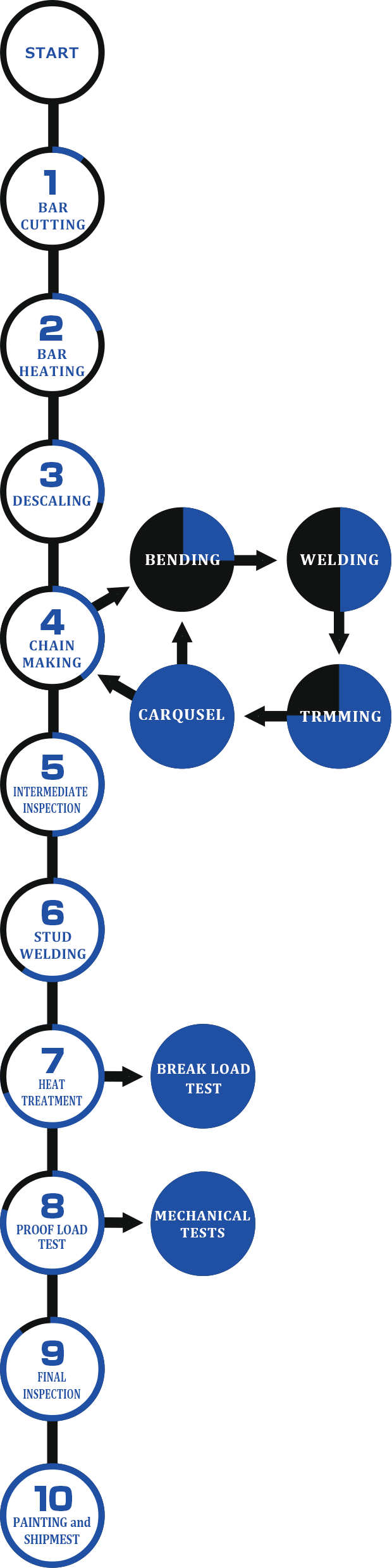
Chain Manufacturing Process Outline Drawing
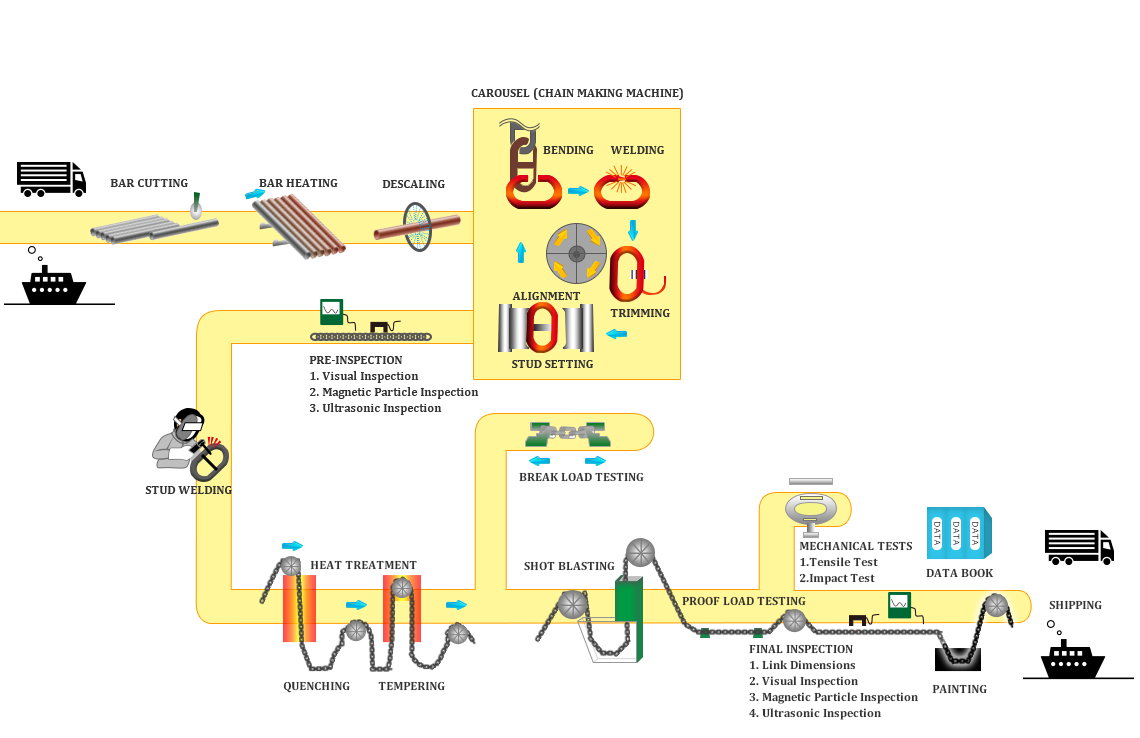

*
By placing the cursor on the character in the image, you can display details.
BAR CUTTING | Round steel bars for chains that just arrived from a steel manufacturer are cut to required lengths. |
---|---|
BAR HEATING | They are heated to be processed into the shape of chain links. Rotation is applied while heating, so that steel is heated uniformly. |
DESCALING | Scales (oxides etc.) on the surface of steel bars are removed by spraying highly pressurized water. |
CHAIN MAKING | Long chains are manufactured by implementing the processes in the order of: BENDING → WELDING → TRIMMING → ALIGNMENT & STUD SETTING → / BENDING→... |
BENDING | Heated steel bars are bent into the shape of chain link. During the first process workpieces are bent into the shape of the letter J, during the second process ? into the shape of a C. When being bent into the C-shape, the link is connected to the previous chain link. |
FLASH BUTT WELDING | We conduct flash butt welding, one of our special processes, on the end surface of a link bent into the C shape. In this process, a flash is generated at the end surface and heat is applied, then once the whole piece is in a molten state, the welding is finished by pushing the ends together. Various parameters of each link such as voltage, current, time, etc. are controlled by a computer. |
TRIMMING | Scraping off protruding parts (burrs) including the oxides from the welding process. |
ALIGNMENT & STUD SETTING | Chain links are shaped into the standard size. In case of a chain with studs, studs are inserted at this time and pushed it into each link and fixed. |
PRE-INSPECTION | Checks for defects and flaws during the manufacturing process are carried out immediately. |
STUD WELDING | In case of marine chains, studs are welded to prevent them from falling out. |
HEAT TREATMENT | We perform vertical continuous heat treatment, which is our special process. QUENCHING and TEMPERING are done continuously by passing chain links through a vertical furnace. By making this a continuous process, it is possible to apply heat treatment of uniform quality to the entire chain. This process determines the strength and toughness of the chain, so it is a very important process. |
PROOF LOAD TESTING | A confirmation of the durability, under the technical standards for ship construction & operation, to the whole chain that has undergone heat treatment, to ensure no deformation & damage. |
BREAK LOAD TESTING | Adding weights above the proved load to some random chain samples to check whether damage occurs. |
MECHANICAL TESTS | Tensile test and Charpy impact test on test pieces collected from some random samples of the chain for the mechanical nature (such as strength & tenacity) of the chain |
FINAL INSPECTION | Visual confirmation, non-destructive tests and size measurement to all chain items underwent the proof load testing for any flaw as the final inspection. |
PAINTING & SHIPPING | Chains that have gone through all inspections are painted and shipped. |